Equipment Details
Pump Make & Model
Grundfos NBG150-125-250/236 X-E2-X-BQQE
Reported Issue
The client reported that the pump was excessively noisy during operation.
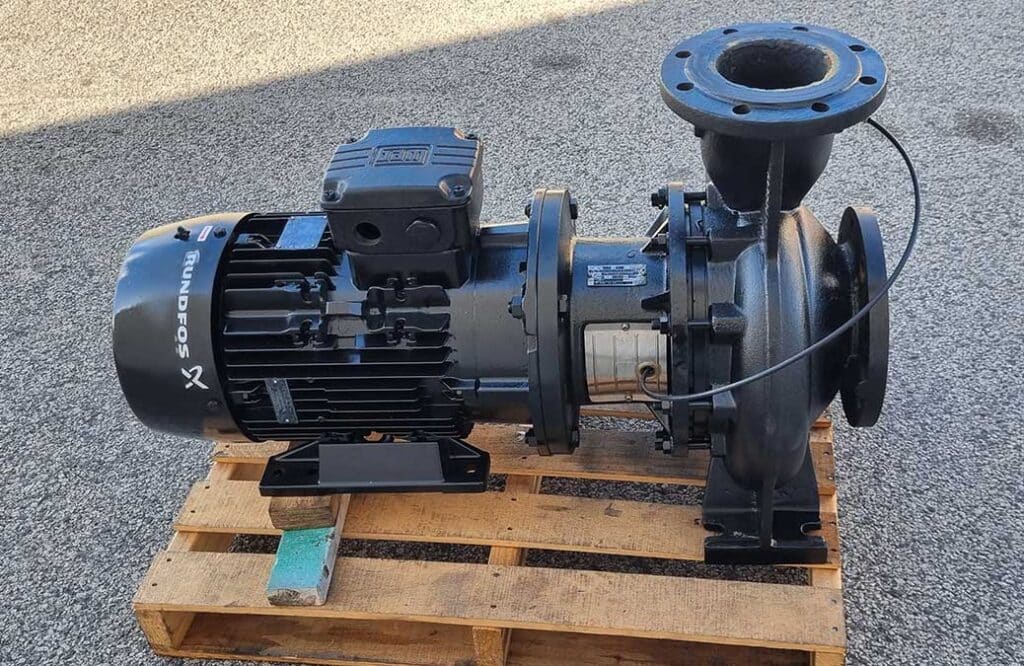
Inspection & Findings
Upon attending the site, our technician confirmed that the noise was mechanical in nature. The pump was subsequently removed and transported to our service centre for a comprehensive assessment.
During the strip-down and inspection, the following issues were identified:
- Bearings: Early stages of bearing failure were detected. The degraded bearings have allowed the impeller to move, resulting in wear to the wear rings, which is contributing to the noise.
- Pump Housing: Internal corrosion was noted throughout the pump housing.
- Stub Shaft: The area where the mechanical seal is seated has significant pitting. This will require machining and the fitting of a sleeve.
- Seal Housing: The seat for the stationary half of the mechanical seal is pitted and will also require machining and sleeving.
- Impeller Efficiency Rings: Both the front and rear efficiency rings are worn. These can be machined to a smooth finish.
- Wear Rings: The wear rings in the volute and seal housing are worn and will need to be manufactured anew to suit the machined components.
Recommended Repairs
- Machine and sleeve the stub shaft and seal housing.
- Machine the impeller efficiency rings to restore smooth operation.
- Manufacture and fit new wear rings in the volute and seal housing.
- Replace the mechanical seal, O-rings, lip seals, and motor bearings.
- Sandblast the internal casing and apply a Loctite ceramic coating to protect against future corrosion and extend the lifespan of the cast iron housing.
Conclusion
Complete Pump Overhaul – Restored to Peak Performance
This pump was fully repaired in line with our proposal. Housings were grit blasted and internally coated with Loctite Brushable Ceramic for enhanced protection.
The impeller’s efficiency rings were precision-machined to a smooth, square tolerance. We machined and sleeved the stub shaft, and fitted newly machined bronze wear rings into both the seal plate and volute. The mechanical seal seat was also machined and sleeved.
Bearings and seals in the electric motor were replaced. The pump was fully reassembled with all tolerances and clearances checked.
A full performance test confirmed smooth operation and hydraulic output within spec (see below curves)
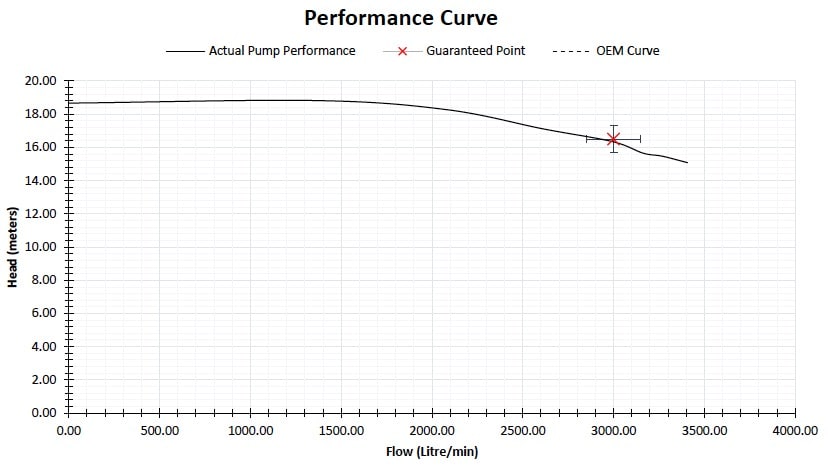
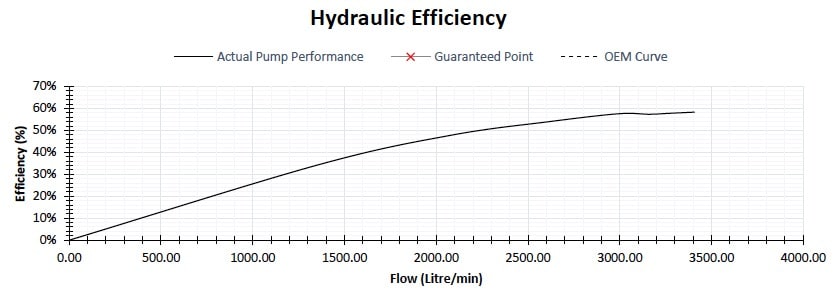
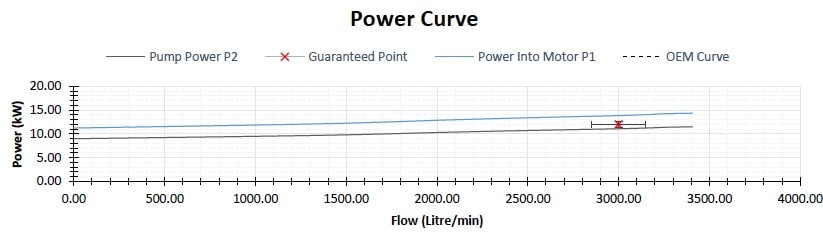